NeedleJeans Production Team Ensuring Consistent Quality
At NeedleJeans we pride ourselves on delivering top quality clothing with every production order. We understand that quality control really means quality assurance. This is why we employs an effective yet simple quality control process to ensure you receive high quality clothing with as few errors as humanly possible.
And if we’ve made a mistake, we’ll simply correct it.
On this page we’ve provided an easy-to-understand explanation of how our quality control process works.
“Specialty Makes Perfect.”
– Jason Xie
NeedleJean’s quality control process uses a methodical human-based approach. During your production, individual pieces are pulled from the production line at random to check that the production is going as planned. Once your entire production is completed, your Production Manager along with our production team check every piece against your tech packs.
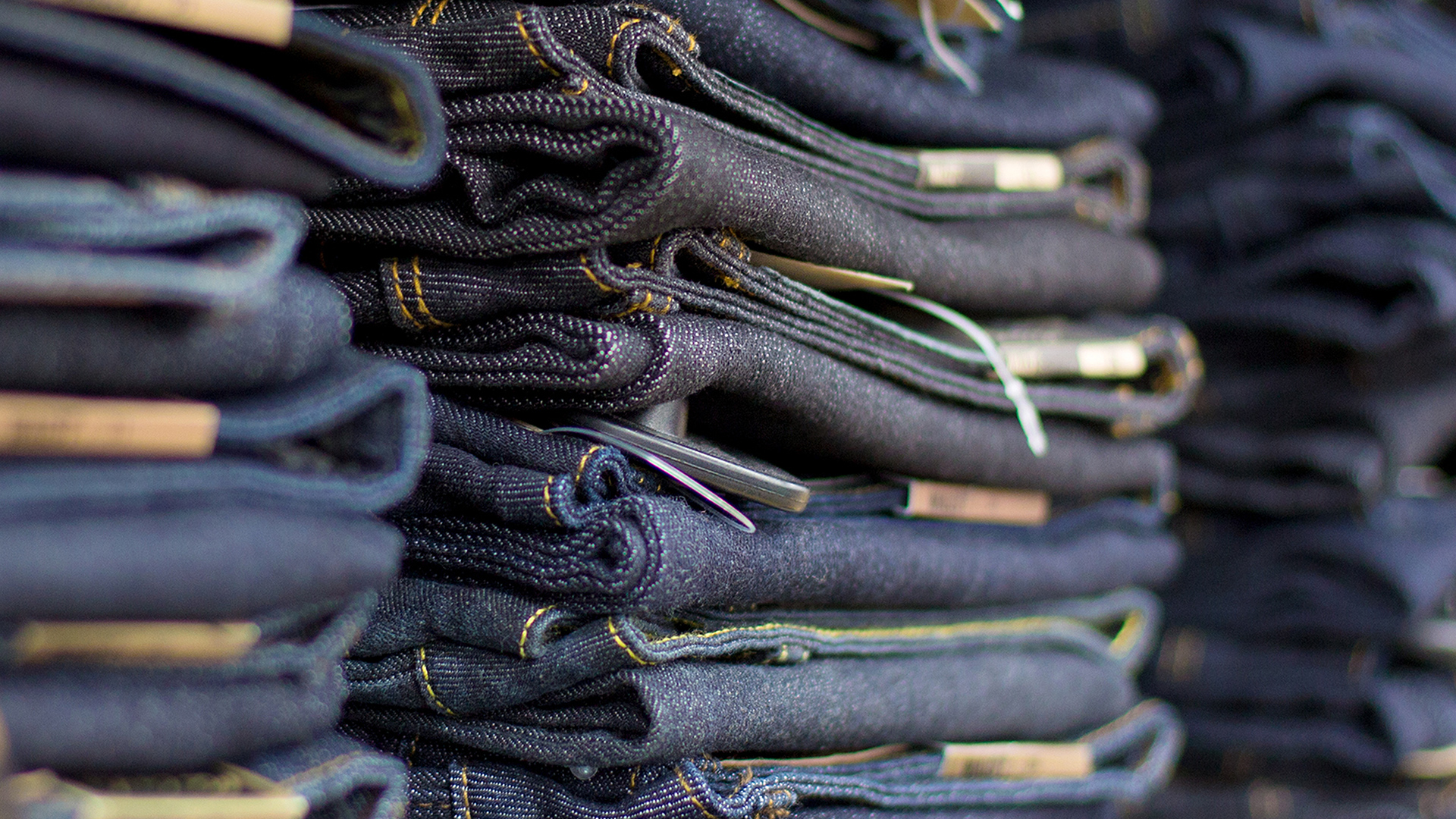

During the quality control process, we check for a variety of criteria. Each piece must pass this checklist otherwise it is sent back for review. The production team checks the quality of stitching, fabric performance, embroidery, printing, dyeing, the quality and strength of all hand-work, material applications, labels and tags quality, and also for the accuracy of seam-to-seam measurements.
It’s important to remember that we’re all human, and even though our main production and quality control processes are robust, once in a while there can be errors that we missed during the QC process. In the unlikely event that you receive your completed production order and a piece has errors, we’ll offer to either repair the affected clothing item(s) or replace it. Simply let your Production Manager know within 7 days of receiving your order.
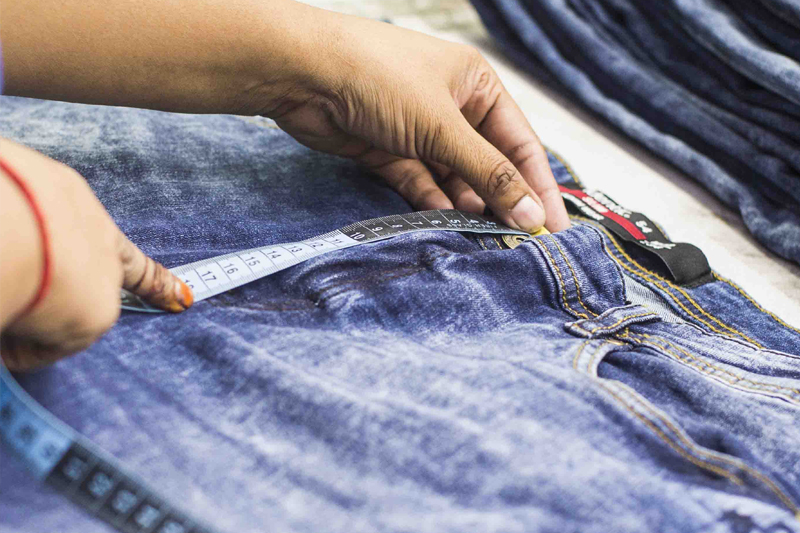
Updates
New Stories
OUR CLIENTS
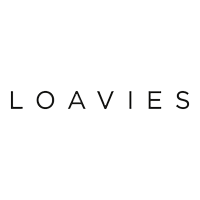
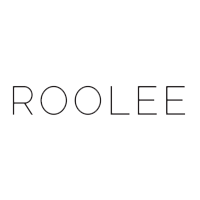
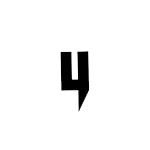
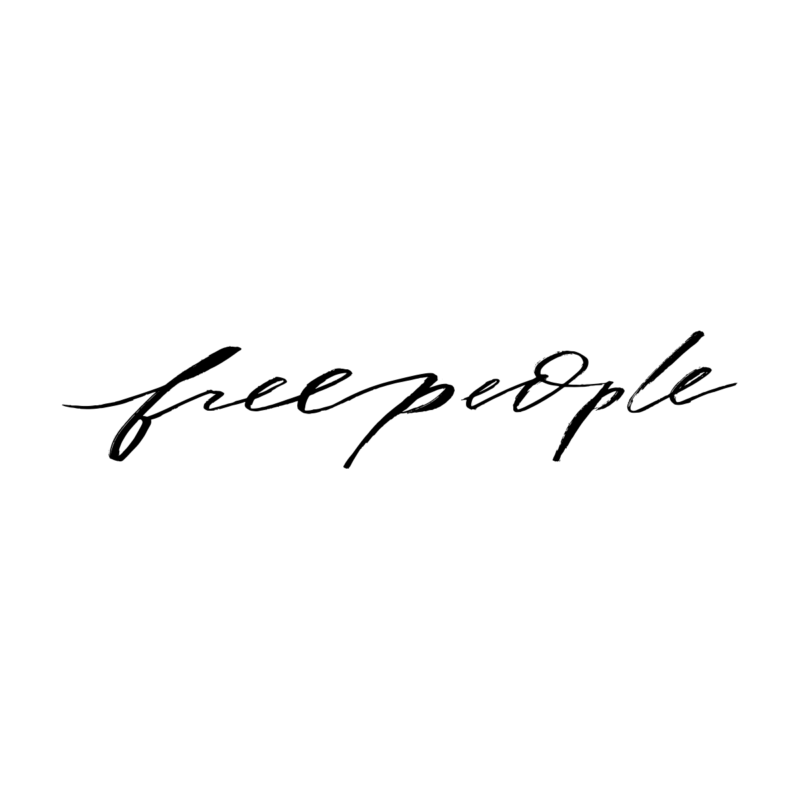

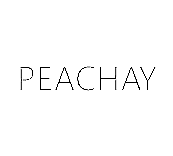